We hope you love the products we recommend and just so you know that as an Amazon Associate EngineHoist.net may earn from qualifying purchases.
Usually, engine hoist are pretty reliable. However, they aren’t entirely foolproof. Many times, an engine hoist will not lift.
This guide is designed to help you diagnose the possible causes and provide straightforward solutions to get your hoist – and your project – back on track.
Whether your hoist is suffering from hydraulic fluid problems, seal leaks, or pump issues, or maybe your engine hoist slowly drops – we have you covered. So, buckle up and get ready to delve into the world of engine hoist troubleshooting with these three practical and action-oriented steps.
Table of Contents
Engine hoist will not lift..
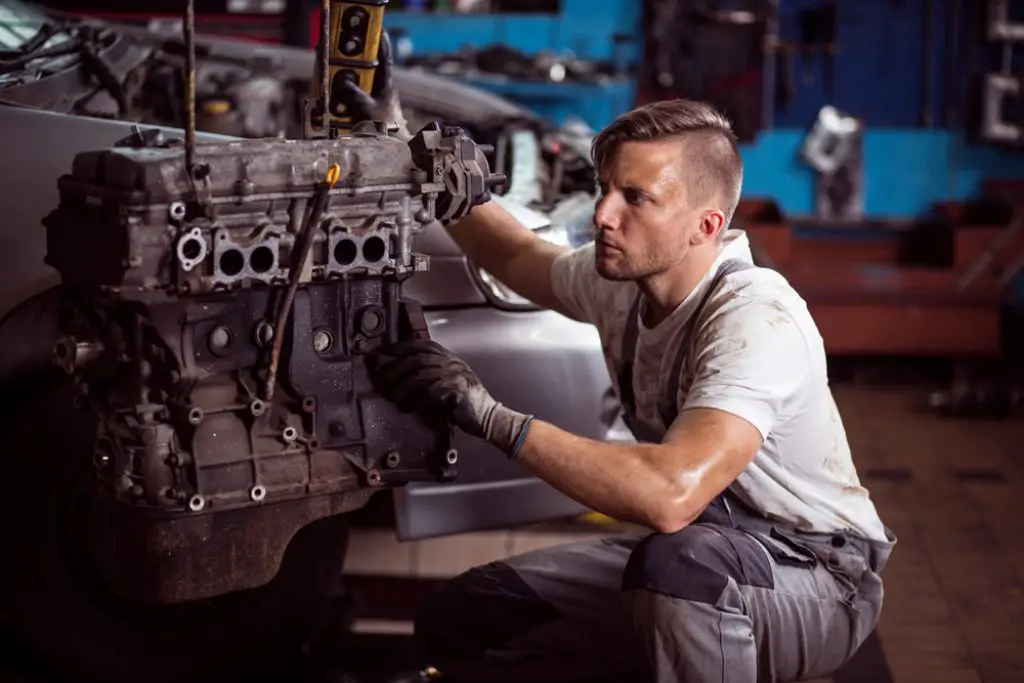
Several reasons might make it so that your engine hoist will not lift. Here are some potential problems and their explanations:
- Hydraulic Fluid Problems: The hydraulic fluid may be low or old. In a hydraulic engine hoist, the fluid is necessary to create the pressure that lifts the engine. Check the fluid levels and quality; if it’s too low, there might not be enough pressure to lift the engine. If the fluid is old or contaminated, it might not function properly.
- Seal Leaks: Engine hoists rely on hydraulic systems, which utilize a series of seals to maintain pressure. If any of these seals have failed or are leaking, the hoist may not lift.
- Pump Issues: The pump could be faulty or damaged, leading to insufficient hydraulic pressure. The pump drives the hydraulic fluid and creates the pressure necessary to lift the engine. We will outline engine hoist pump repair in the sections below.
- Broken or Damaged Parts: Parts such as the lifting arm, chains, or hooks might be broken, damaged, or worn out. These parts are responsible for lifting and holding the engine, and if they’re compromised, they may not perform properly.
- Overload: If the engine’s weight exceeds the hoist’s maximum load capacity, the hoist will not be able to lift it. Always ensure you’re not trying to lift more than the hoist’s rated capacity.
- Air in the Hydraulic System: If there’s air in the hydraulic system, it could prevent the hoist from working properly. Hydraulic systems are designed to be filled with incompressible fluid, and the presence of air, which is compressible, can reduce the system’s ability to exert force.
- Worn Out or Damaged Pistons: If the pistons in the hydraulic system are worn out or damaged, they may not be able to create the necessary pressure to lift the engine.
The two main causes that I have found working with engine hoists frequently, is the following:
- The pressurised expansion and subsequent eruption of a seal
- Low hydraulic pressure fluid, or lack of hydraulic fluid.
While these two problems might be interrelated, they are the primary causes of why the engine hoist will not lift.
Before we help you understand how to solve this problem, it is time to look into how the engine hoist works.
How Does a Hydraulic Engine Hoist Work?
The hydraulic engine hoist works very similar to a normal crane. Once you attach the engine to it, the hydraulic cylinders work because of the pressurized hydraulic fluid needed to lift the piston, which in turn lifts the engine attached to the arm.
When you’re lowering the engine, the engine hoist will open the bleed valve resulting in the low pressure of the hydraulic fluid. Therefore, the engine will gradually move in the opposite direction because of gravity and will be lowered.
How Do You Fix an Engine Hoist?
Now that you understand the mechanism that drives an engine hoist, if it’s just not working for you, lets learn about how to fix the problem.
How to Reseal the Hydraulic Cylinder
The seal of the hydraulic cylinders determines the pressure of the hydraulic fluid. If you blow up the seal, the hydraulic fluid will start leaking. In that case, the pressure will not be maintained in the cylinders, so you won’t be able to lift the attached engine appropriately.
The simplest way is to reseal it. You might have to buy the sealing apparatus once again and install it. In most cases, repairing a blown-up seal is not possible. That is why replacing is the only solution.
Here is a step by step guide to reseal the Hydraulic Cylinder:
- Inspect the hydraulic cylinder: Check if there are any loose parts such as a nut on the rod. If so, these will need to be repaired. Also, consider installing a seal kit if the tractor has significant usage.
- Dismantle the hydraulic cylinder: Carefully take apart the cylinder, making sure not to damage the rod. Pay special attention to the white piece or ‘baron’ that slides on the inside of the cylinder and the piston’s seal.
- Replace the seals and o-rings: Each cylinder will have a nut holding the piston to the rod. If the piston is loose on the rod, replace the o-ring that helps to keep oil from sliding past and underneath the piston.
- Install the new seal on the piston: Put the new seal from your engine hoist seal kit on the piston along with a new bearing. Make sure you put the seals in the correct order, or the piston won’t function properly.
- Reinstall the piston onto the rod: Apply some grease on the inside of the seal before sliding the piston onto the rod. This reduces the likelihood of tearing the seal. Tighten the rod with an appropriate torque (around 120 pounds was suggested in the transcript).
- Inspect the barrel: Before reassembling everything, inspect the barrel for any damage. If there are any rough patches or spots, it might not be worth replacing the packing as it could cause more leaks in the future.
- Reassemble the hydraulic cylinder: After making sure all the parts are in order, carefully reassemble the hydraulic cylinder. Apply some grease on the inside of the barrel to protect the new seals. Tighten the cylinder back into place.
- Test the hydraulic cylinder: Once you’ve reassembled everything, test the cylinder for any external leaks. Try to move the bucket a few times to clear any air out of the system. Apply pressure on the bucket to see if it rolls back as expected.
Remember, always consult a professional or your tractor’s user manual if you’re unsure about any steps in this process. Working with hydraulic systems can be complex and dangerous if not done correctly.
Change the Bleed Valves to Avoid Low Pressure:
There is a bleed valve in every engine hoist.
Its job is to release the pressure on the hydraulic fluid. However, if the bleed valve is faulty, it will release the pressure at the wrong time, and the hoist will not lift at all.
The easiest solution to fix this problem is to change the bleed valve.
Changing a bleed valve on an engine hoist involves a relatively straightforward process. However, please keep in mind that safety should be your top priority, and you should always have your user’s manual on hand to refer to.
Here are the general steps:
- Safety Precautions: Ensure that the hoist is not supporting any load and is in a safe, stable position. Ensure you’re wearing appropriate personal protective equipment, such as gloves and safety glasses.
- Locate the bleed valve: The bleed valve (also known as the release valve) is usually located on the hydraulic pump of your engine hoist.
- Remove the Old Bleed Valve: To remove the old valve, use an appropriate wrench or socket that fits the valve. Turn counterclockwise to loosen it. Once loose, you can unscrew it by hand. Be careful not to allow any hydraulic fluid to leak out onto your skin or into your eyes.
- Prepare the New Bleed Valve: Before installing, it’s a good idea to wrap the threaded part of the new valve with Teflon tape. This helps ensure a good seal and prevent leaks.
- Install the New Bleed Valve: Screw in the new valve by hand at first to prevent cross-threading, then use your wrench or socket to tighten it. Be sure not to over tighten it as this could damage the threads.
- Check for Leaks: After installing the new bleed valve, you’ll want to check for any potential leaks. Pump the hoist a few times and look for any leaking fluid around the new valve.
- Test the Hoist: Finally, test the hoist with a light load to ensure everything is working properly. The hoist should raise and lower smoothly.
Remember, if at any point you feel uncomfortable performing these steps, or if your hoist is not functioning correctly after replacing the valve, consult with a professional or the hoist manufacturer.
How Do You Fill an Engine Hoist with Hydraulic Fluid?
Usually, low or no hydraulic fluid is the reason why the engine hoist will not lift. This is an easy problem to fix. You can buy the hydraulic fluid from the hardware store and refill it.
Here is a step-by-step procedure to refill the hydraulic fluid.
Procedure to Refill Hydraulic Fluid in an Engine Hoist:
- Locate the plug of the hydraulic fluid reservoir: This plug will typically be on top of the reservoir.
- Remove the plug: Using a pair of wire clippers, carefully squeeze the plug and then pull it out to open the reservoir.
- Prepare the filling mechanism: Take a silicone hose and fit it to the reservoir’s opening. Attach a small funnel to the other end of the hose. Cut the hose to a usable length if needed. To assist with filling, suspend the funnel with a piece of wire or similar so you can have both hands free.
- Prepare the hydraulic fluid: Fill a small, manageable container with the hydraulic fluid to make it easier to pour into the funnel. Using a smaller container will provide more control when pouring.
- Fill the reservoir: Begin to pour the hydraulic fluid into the funnel slowly, making sure the fluid flows down the hose and into the reservoir. You may want to check your manual to find out the engine hoist oil capacity.
- Check the fluid level: Continue pouring until you see fluid beginning to come out of the reservoir. This indicates the reservoir is full.
- Operate the hoist: After the reservoir is filled, operate the hoist up and down a few times to work the new fluid into the system. This also allows for checking if more fluid needs to be added.
- Retract the hoist and remove the filling mechanism: After operating the hoist, retract it to its original position and remove the funnel and hose.
- Replace the plug: Use a tool or your fingers to carefully press the plug back into the opening of the reservoir. Make sure it is secure and fully inserted.
- Test the hoist: Finally, test the operation of the hoist to make sure it’s working properly and there are no leaks.
How Do you Bleed an Engine Hoist Jack?
Procedure for Bleeding an Engine Hoist Hydraulic Circuit:
- Identify the Bleed Port: Find the bleed port on the hydraulic circuit of your engine hoist. It could be a fitting cap or plug without an elastomeric seal, such as a JIC fitting or tube fittings.
- Charge the Circuit: Charge the hydraulic circuit at a low pressure.
- Loosen the Fitting: Start at the fitting that is farthest from the power supply. Loosen this fitting enough to allow a steady flow of oil to come out.
- Observe the Oil: Watch the oil that is flowing out. If there’s air in it, the oil will appear milky due to small bubbles.
- Allow the Oil to Flow: Let the oil flow until it runs clear, indicating that the air has been bled out.
- Tighten the Fitting: Once the oil is clear, tighten the fitting back up.
- Repeat as Needed: If your hydraulic circuit has devices or features that limit or divide the flow, you may need to bleed the circuit at more than one location. If this is the case, repeat the process, working your way back towards the power supply.
- Seek Help if Needed: If you have any questions or issues with the process, don’t hesitate to contact customer support for assistance.
Remember to always follow safety procedures and use appropriate protective equipment when working with hydraulic systems.
Final Words
Instead of wondering why the engine hoist will not lift, it is good to follow our guide above and try the solutions we have listed. Check out the videos that have some great explainations for why your engine hoist will not lift too!
Lets get your workshop humming along again!
How do you bleed the air out of an engine hoist?
To bleed the air out of an engine hoist, you need to first locate the bleed valve or fitting. Charge the hydraulic circuit at low pressure and begin at the fitting farthest from the power supply. Loosen the fitting to allow a steady flow of oil until it runs clear, indicating the air has been expelled. If the hoist has features that limit or divide the flow, repeat the process at each point, working back towards the power supply. After the oil runs clear at all points, tighten the fittings.
What is the problem with the hydraulic jack?
Problems with a hydraulic jack can vary widely, but common issues include hydraulic fluid leaks, air entering the system (which requires bleeding), wear and tear on seals and components, or mechanical damage. It’s also possible that the hydraulic fluid is old or contaminated, which can affect the jack’s performance. If the jack isn’t lifting properly, these are some potential issues to investigate.
What kind of hydraulic fluid for engine hoist?
Hydraulic fluid specially designed for hydraulic jacks is recommended for engine hoists. These fluids are typically labeled as “jack oil.” However, in some cases, automatic transmission fluid (ATF) or universal tractor fluid can be used. It’s crucial to check the manufacturer’s specifications for the correct type and grade of hydraulic fluid to use.
How do you put oil in a hydraulic engine hoist?
To put oil in a hydraulic engine hoist, locate the fill plug and remove it. Use a funnel connected to a silicone hose to pour the oil into the fill hole. Make sure to pour slowly and stop once the oil starts coming out of the fill plug, indicating that it’s full. Then replace the plug, pump the jack a few times to work the oil in, and check the oil level again. Fill more if necessary, then replace and secure the fill plug.